Part II: Design Criteria: Problems And Solutions
B. Ion Optics, Sharp Edges, Points, Cracks and Other Sources of
Grief (continued)
iv. The Electrodes : Solutions
Thermal discontinuities, like electrcal ones, are points of massive energy
transport. This being the case, dewars have to be polished smooth
to prevent heat loss. Furthermore, they are pumped down to vacuum,
sealed and designed to remain that way for decades. The solder spattered
on the outer surface of the inner shell of this
dewar occured while de-soldering the hemispherical outer shell. The
vacuum, which was about 40 years old, was still good enough to suck
the molten solder inside! It is reasonable to suppose that this dewar
can be adapted to replace both the bell jar and the anode, assuring better
ion optics and vacuum performance. The shells will probably be low
temperature brazed back together. This will allow for future disassembly
and requires less flux with the copper shell.
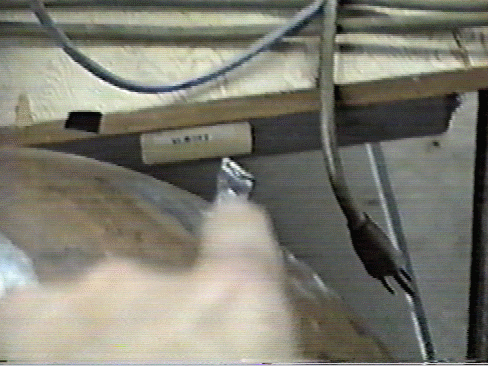
This crimped and soldered "tit" was where the original dewar was pumped
down, then sealed.
A very similar spherical dewar to the one "harvested" for the purpose of
this experiment. The inner diameter of the copper shell is 19&3/8",
more than enough, allowing a breakdown voltage of 1kV/mm to assure that
the 5" electrode currently used as the anode in the demo model, will have
plenty of room for very high potential!
As far as the demo model goes, a new cathode was cast, using a lost wax
procedure. It is about, 87% transparent, still low, but within Miley's
absolute minimum of 80% necessary to attain fusion.
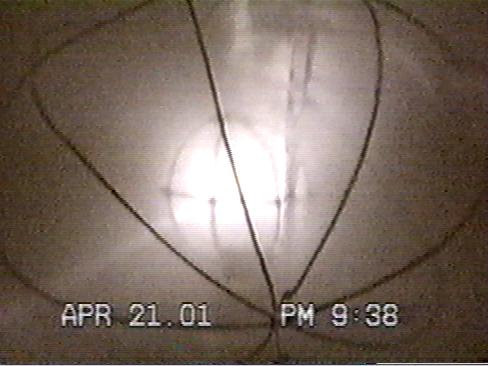
The finished product in action above.
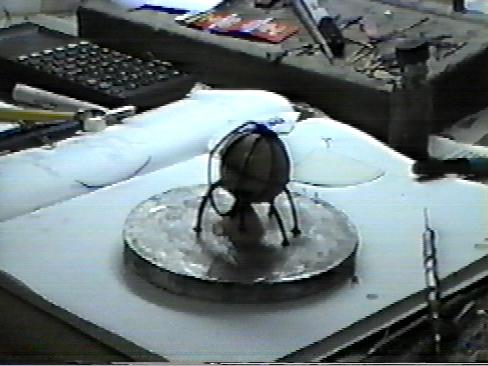
The 20 gauge wax wire grid on the sprue form, ready to be invested, burnt
out, then induction cast. The Cr-Co-Mo alloy has a melting point
of about 1500 F, a disadvantage but one must get it hot enough to melt
first. T-304 stainless melts at only 1800 F anyway.
